INCONEL 600 (UNS N06600 /N.º de artículo 2.4816)
Introducción del producto
La aleación 600 es excelente para diversos usos en entornos con temperaturas extremadamente altas y alta corrosión. Es una aleación de níquel-cromo diseñada para usarse desde temperaturas criogénicas hasta temperaturas elevadas de hasta 1093 °C (2000 °F).
El alto contenido de níquel de la aleación le permite resistir la corrosión de una serie de compuestos orgánicos e inorgánicos.
La estructura de grano más fino del tubo acabado en frío, además, aporta una mejor resistencia a la corrosión, lo que incluye valores más elevados de resistencia a la fatiga y al impacto.
La aleación 600 es relativamente resistente a la mayoría de las soluciones salinas neutras y alcalinas y se utiliza en algunos entornos cáusticos. Resiste el vapor y las mezclas de vapor, aire y dióxido de carbono.
Aplicaciones:
Centrales nucleares.
Intercambiadores de calor.
Vainas de termopar.
Equipos de procesamiento químico y de alimentos.
Tubos de craqueo de dicloruro de etileno (EDC).
Conversión de dióxido de uranio en tetrafluoruro en contacto con ácido fluorhídrico.
Producción de álcalis cáusticos particularmente en presencia de compuestos de azufre.
Recipientes de reactor y tubos de intercambiadores de calor utilizados en la producción de cloruro de vinilo.
Equipos de proceso utilizados en la producción de hidrocarburos clorados y fluorados.
En reactores nucleares, se utiliza en componentes como tubos de entrada de barras de control, componentes y sellos de la vasija del reactor, secadores de vapor y separadores de vapor en reactores de agua en ebullición. En reactores de agua a presión, se utiliza en tubos guía de barras de control y placas deflectoras de generadores de vapor, entre otros.
Sellos, ventiladores y accesorios de retorta de horno.
Hogares de rodillos y tubos radiantes, especialmente en procesos de nitruración de carbono.
Solicitud
La estructura de grano más fino del tubo acabado en frío, además, aporta una mejor resistencia a la corrosión, lo que incluye valores más elevados de resistencia a la fatiga y al impacto.
La aleación 600 es relativamente resistente a la mayoría de las soluciones salinas neutras y alcalinas y se utiliza en algunos entornos cáusticos. Resiste el vapor y las mezclas de vapor, aire y dióxido de carbono.
Especificaciones del producto
ASTM B163, ASTM B167
Requisitos químicos
Aleación 600 (UNS N06600)
Composición %
Ni Níquel | Cu Cobre | Fe hierro | Mn Manganeso | C Carbón | Si Silicio | S Azufre | Cr Cromo |
72.0 minutos | 0,50 máximo | 6.00-10.00 | 1.00 máximo | 0,15 máximo | 0,50 máximo | 0,015 máximo | 14.0-17.0 |
Propiedades mecánicas | |
Fuerza de fluencia | 35 Ksi mín. |
Resistencia a la tracción | 80 Ksi mín. |
Alargamiento (2" mín.) | 30% |
Tolerancia de tamaño
sobredosis | OD Toleracné | Tolerancia WT |
Pulgada | mm | % |
1/8" | +0,08/-0 | +/-10 |
1/4" | +/-0,10 | +/-10 |
Hasta 1/2" | +/-0,13 | +/-15 |
1/2" a 1-1/2", excl. | +/-0,13 | +/-10 |
1-1/2" a 3-1/2", excl. | +/-0,25 | +/-10 |
Nota: La tolerancia se puede negociar según los requisitos específicos del cliente. |
Presión máxima permitida (unidad: BAR) | ||||||||
Espesor de la pared (mm) | ||||||||
0.89 | 1.24 | 1.65 | 2.11 | 2.77 | 3.96 | 4.78 | ||
Diámetro exterior (mm) | 6.35 | 451 | 656 | 898 | 1161 | |||
9.53 | 290 | 416 | 573 | 754 | 1013 | |||
12.7 | 214 | 304 | 415 | 546 | 742 | |||
19.05 | 198 | 267 | 349 | 470 | ||||
25.4 | 147 | 197 | 256 | 343 | 509 | 630 | ||
31.8 | 116 | 156 | 202 | 269 | 396 | 488 | ||
38.1 | 129 | 167 | 222 | 325 | 399 | |||
50.8 | 96 | 124 | 164 | 239 | 292 |
Certificado de honor
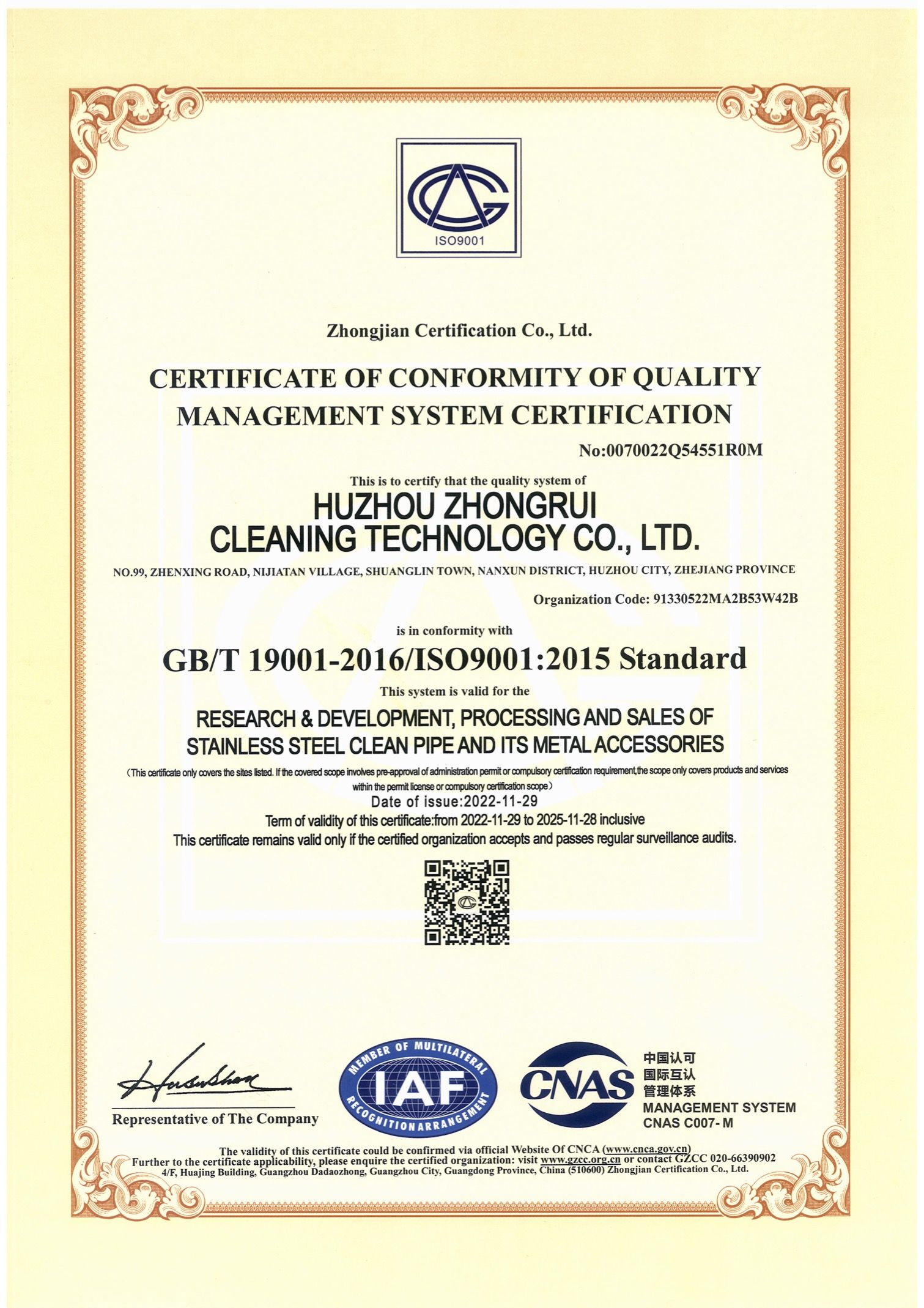
Norma ISO9001/2015
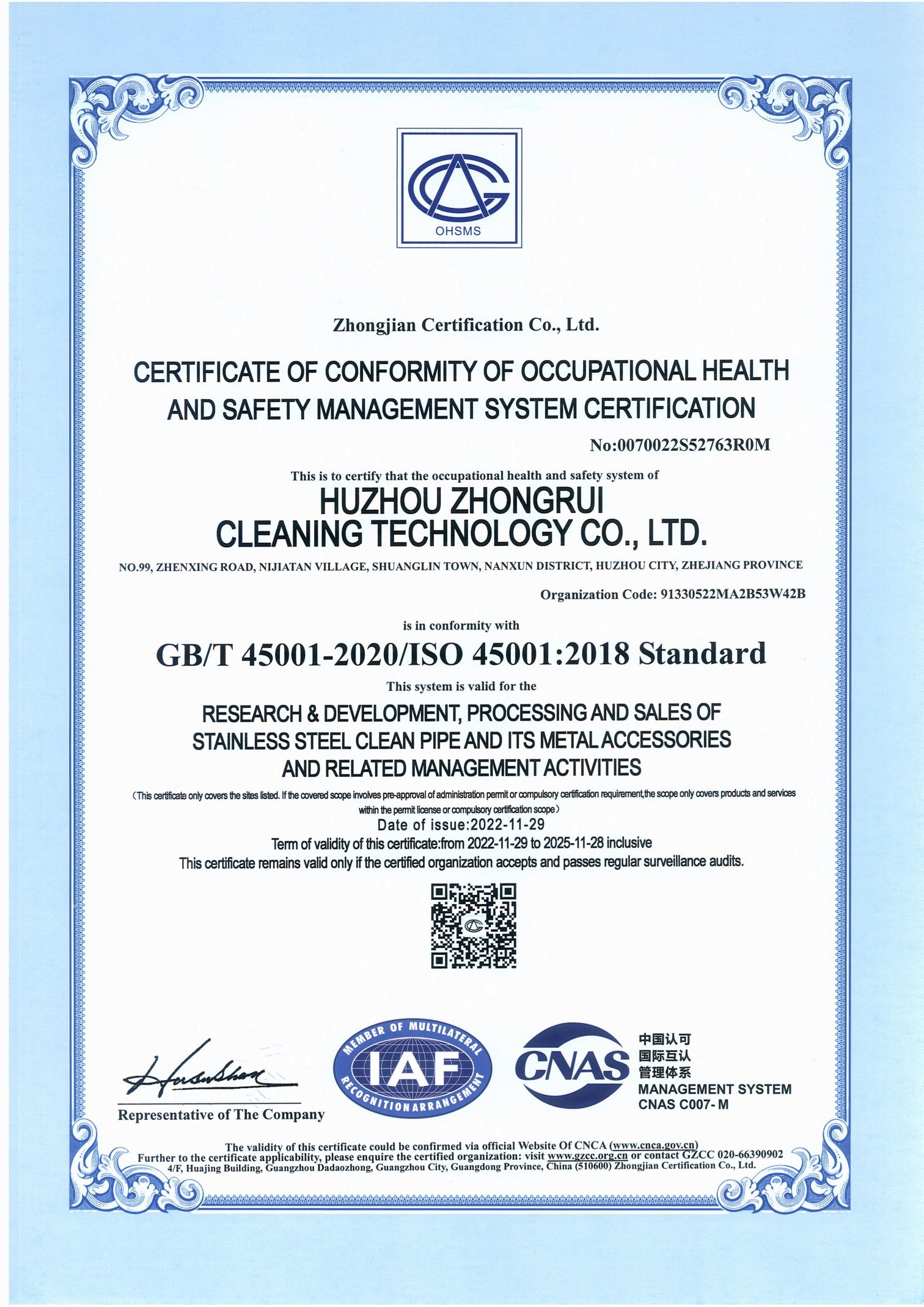
Norma ISO 45001/2018
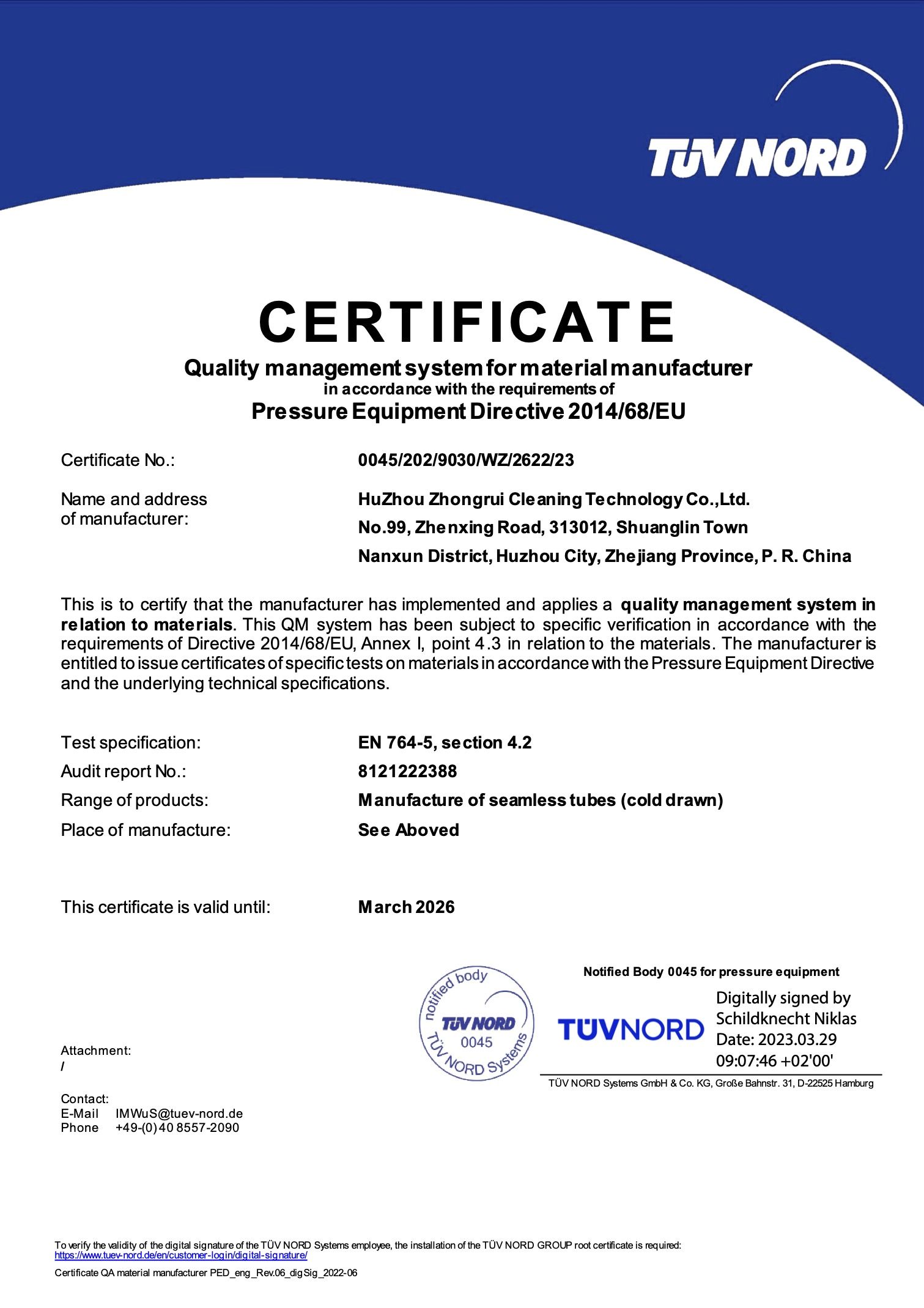
Certificado PED
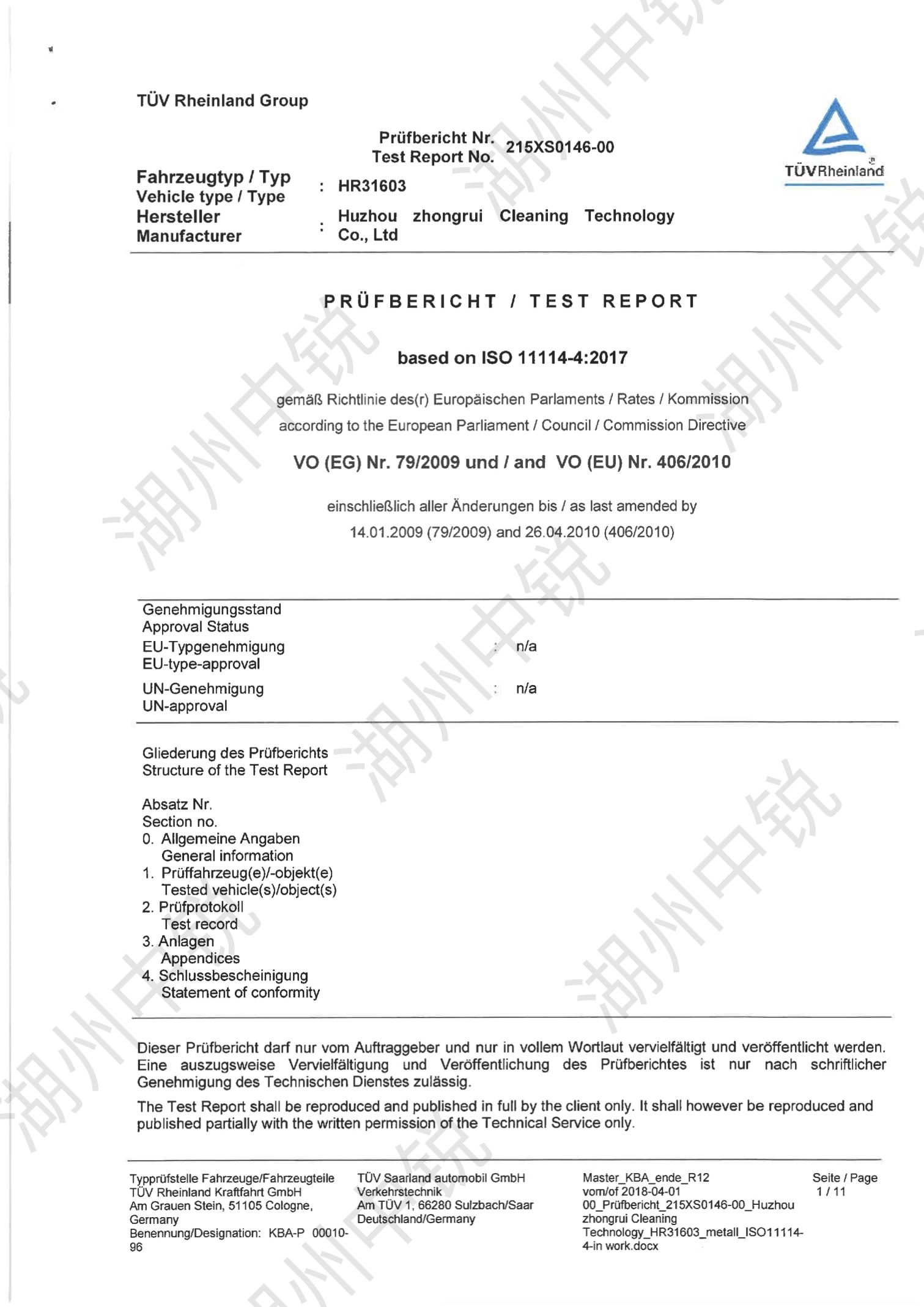
Certificado de prueba de compatibilidad de hidrógeno TUV
No. | Tamaño (mm) | |
sobredosis | Gracias | |
Rugosidad de la superficie interior del tubo BA Ra0.35 | ||
1/4″ | 6.35 | 0.89 |
6.35 | 1.00 | |
3/8″ | 9.53 | 0.89 |
9.53 | 1.00 | |
1/2” | 12.70 | 0.89 |
12.70 | 1.00 | |
12.70 | 1.24 | |
3/4” | 19.05 | 1.65 |
1 | 25.40 | 1.65 |
Rugosidad de la superficie interior del tubo BA Ra0.6 | ||
1/8″ | 3.175 | 0,71 |
1/4″ | 6.35 | 0.89 |
3/8″ | 9.53 | 0.89 |
9.53 | 1.00 | |
9.53 | 1.24 | |
9.53 | 1.65 | |
9.53 | 2.11 | |
9.53 | 3.18 | |
1/2″ | 12.70 | 0.89 |
12.70 | 1.00 | |
12.70 | 1.24 | |
12.70 | 1.65 | |
12.70 | 2.11 | |
5/8″ | 15.88 | 1.24 |
15.88 | 1.65 | |
3/4″ | 19.05 | 1.24 |
19.05 | 1.65 | |
19.05 | 2.11 | |
1″ | 25.40 | 1.24 |
25.40 | 1.65 | |
25.40 | 2.11 | |
1-1/4″ | 31,75 | 1.65 |
1-1/2″ | 38.10 | 1.65 |
2″ | 50.80 | 1.65 |
10A | 17.30 | 1.20 |
15A | 21.70 | 1.65 |
20A | 27.20 | 1.65 |
25A | 34.00 | 1.65 |
32A | 42.70 | 1.65 |
40A | 48.60 | 1.65 |
50A | 60.50 | 1.65 |
8.00 | 1.00 | |
8.00 | 1,50 | |
10.00 | 1.00 | |
10.00 | 1,50 | |
10.00 | 2.00 | |
12.00 | 1.00 | |
12.00 | 1,50 | |
12.00 | 2.00 | |
14.00 | 1.00 | |
14.00 | 1,50 | |
14.00 | 2.00 | |
15.00 | 1.00 | |
15.00 | 1,50 | |
15.00 | 2.00 | |
16.00 | 1.00 | |
16.00 | 1,50 | |
16.00 | 2.00 | |
18.00 | 1.00 | |
18.00 | 1,50 | |
18.00 | 2.00 | |
19.00 | 1,50 | |
19.00 | 2.00 | |
20.00 | 1,50 | |
20.00 | 2.00 | |
22.00 | 1,50 | |
22.00 | 2.00 | |
25.00 | 2.00 | |
28.00 | 1,50 | |
Tubo BA, sin solicitud sobre la rugosidad de la superficie interior | ||
1/4″ | 6.35 | 0.89 |
6.35 | 1.24 | |
6.35 | 1.65 | |
3/8″ | 9.53 | 0.89 |
9.53 | 1.24 | |
9.53 | 1.65 | |
9.53 | 2.11 | |
1/2″ | 12.70 | 0.89 |
12.70 | 1.24 | |
12.70 | 1.65 | |
12.70 | 2.11 | |
6.00 | 1.00 | |
8.00 | 1.00 | |
10.00 | 1.00 | |
12.00 | 1.00 | |
12.00 | 1,50 |